MDIC News
Keep up with the latest news from MDIC
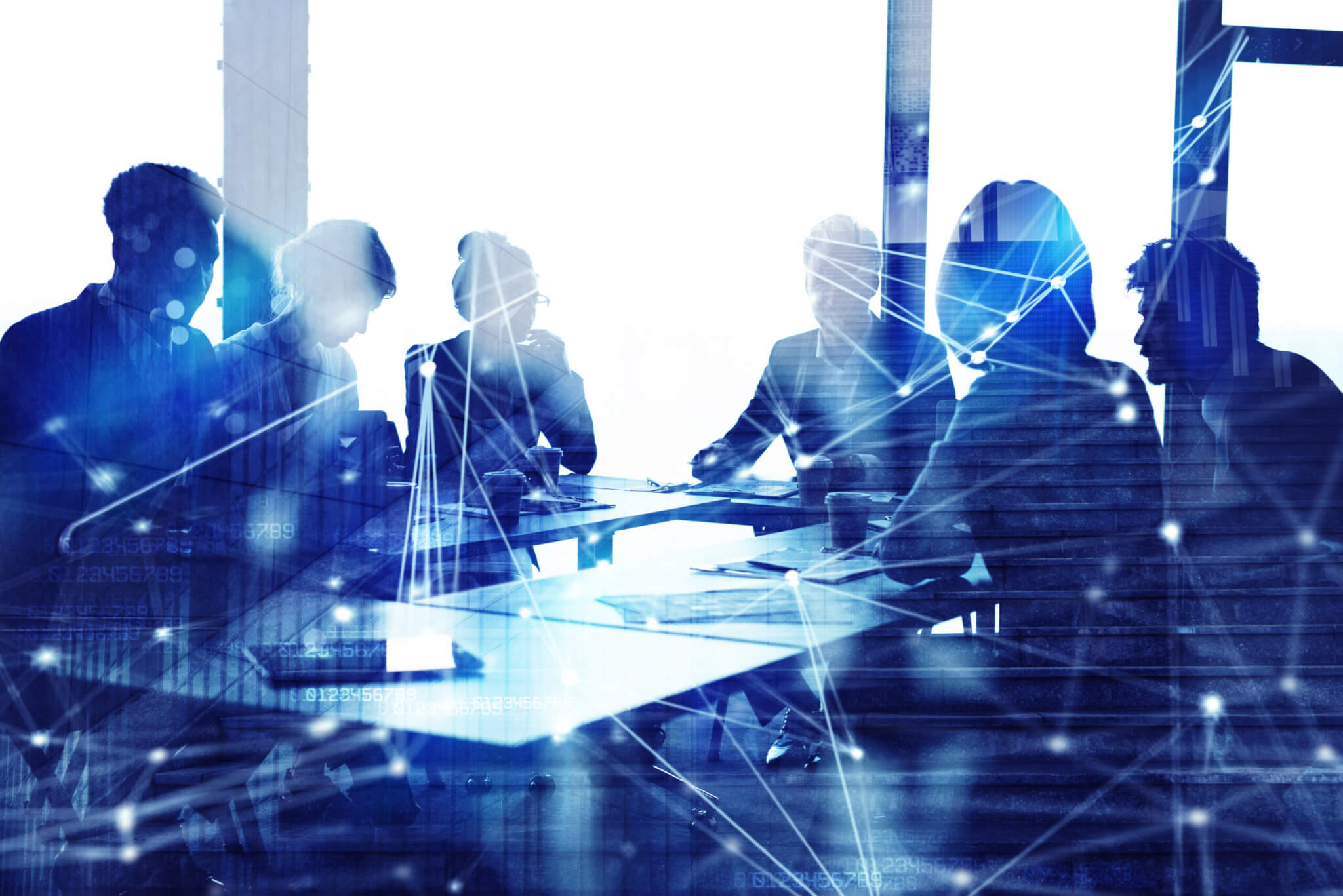
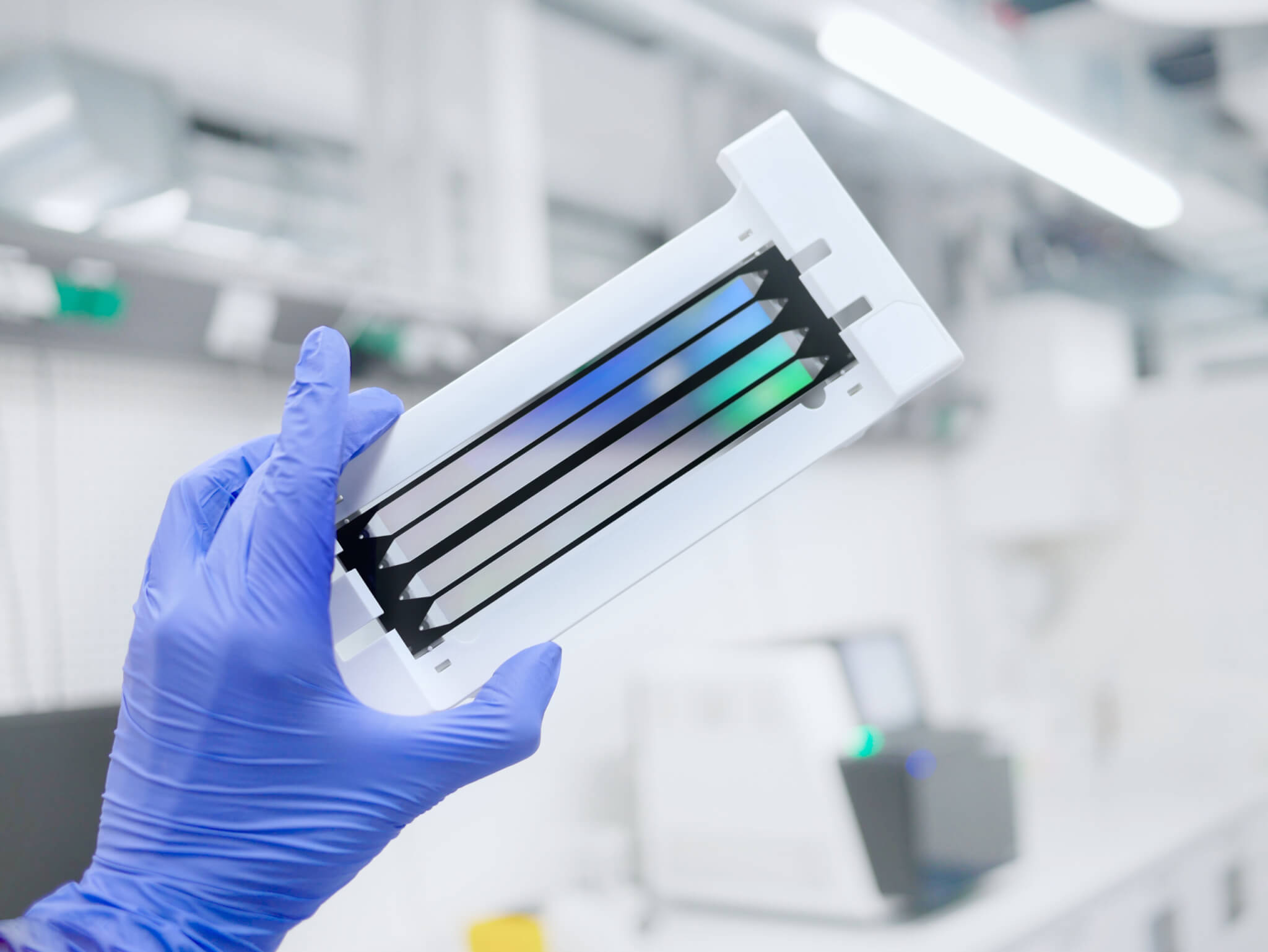
March 19, 2025
Engineered Variant Clones Confirmed for MDIC’s Somatic Reference Sample (SRS) Initiative

March 12, 2025
Contribute to the Future of RWE: NEST Seeks Feedback on Updated Frameworks
NEST is updating its Research Methods and Data Quality Frameworks to improve the rigor and reliability of real-world evidence (RWE) in medical device evaluation, and is seeking public feedback to ensure these frameworks remain valuable…